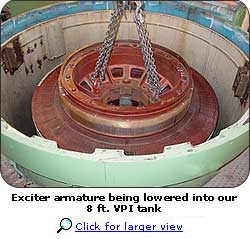
Vacuum Pressure Impregnation
(VPI)
Our 4 separate VPI systems has set us apart from
other motor repair facilities. To our knowledge,
no other motor repair shop in the country has
4 VPI systems under one roof. We have made a considerable
investment in these systems in an effort to offer
our customers the best product for their particular
application.
The
following is a listing of our VPI systems and
the product used in each.
- System #1:
8 ft. VPI System with Dolphon Polyester
Resin.
- System #2:
5 ft. VPI System with Guardian Epoxy Resin.
- System #3:
5 ft. VPI System with Traction/Mining VT
Resin.
- System #4:
3 ft. VPI System with Siemens approved VT
Resin.
For those not familiar with the VPI process, here
is a brief overview of how it works and why it
is beneficial.
The
VPI process most often occurs after the motor
stator has been rewound. The stator is suspended
in the tank and the lid closed. A vacuum is then
pulled until the desired vacuum level is achieved,
then held for a specified period of time.
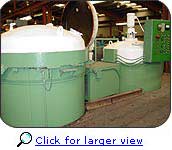 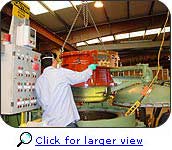
At this time the transfer valve is opened and
the resin is transferred from the storage tank
into the processing tank filling it until the
stator windings are completely immersed. The transfer
valve is then closed and the tank is held under
vacuum for a short period of time. The
tank is then pressurized and held again for a
predetermined time which forces the resin through
the multiple layers of wire and insulation (filling
all voids).
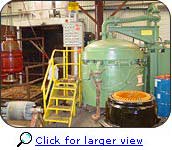 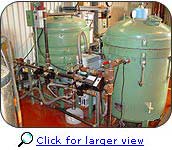
Conventional
varnishes are composed of 50% or more solvent,
which evaporates during the bake cycle and allows
for only a partial fill of these voids. dahl-beck
electric offers four different 100% solventless
resins. These products in conjunction with our
VPI systems provide superior electrical insulation
and a coil system that is impervious to moisture,
contamination and corrosive chemicals. These products
also provide improved cooling characteristics
and a coil that is virtually vibration free.
 |